Advancements in High Voltage Fuse Technology
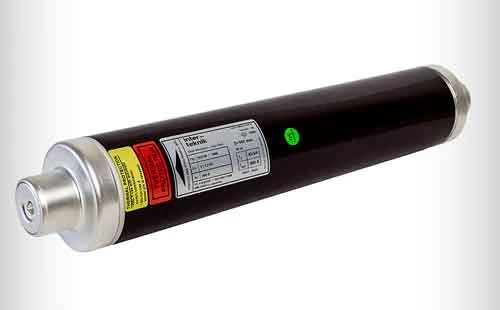
High voltage fuses are integral components in electrical systems, providing protection against overcurrents and short circuits. Recent advancements in materials science and manufacturing processes have significantly improved the performance, reliability, and cost-effectiveness of these fuses. This article explores the latest developments in high voltage fuse technology and their impact on the industry.
Innovations in Fuse Materials
Enhanced Conductive Elements
The core of high voltage fuse technology lies in the materials used for conductive elements. Advances in metallurgy have led to the development of alloys that offer superior electrical conductivity and improved melting characteristics. These materials enhance the fuse's ability to carry nominal currents without degradation and respond more effectively under fault conditions.
High-Performance Insulation
Innovations in insulation materials are crucial for high voltage fuses, especially in terms of thermal and electrical properties. New composite materials and ceramics provide better insulation, withstand higher temperatures, and resist environmental stress, leading to fuses that are more durable and reliable.
Environmentally Resistant Coatings
Coatings that protect against corrosion, moisture, and chemical exposure have seen significant improvements. These coatings extend the life of fuses in harsh environments and prevent premature failures, contributing to the overall reliability of electrical systems.
Manufacturing Process Enhancements
Precision Engineering and Automation
The manufacturing of high voltage fuses has benefited from precision engineering and automation. Advanced manufacturing techniques, such as computer-aided design (CAD) and computer-aided manufacturing (CAM), allow for precise control over the dimensions and properties of fuse components, resulting in products with higher consistency and quality.
Lean Manufacturing Practices
Lean manufacturing practices have been adopted to improve efficiency and reduce waste in the production of high voltage fuses. These methodologies help manufacturers optimize processes, minimize defects, and lower production costs, leading to more cost-effective solutions for customers.
Quality Assurance and Testing
With the adoption of stringent quality control measures and sophisticated testing methods, manufacturers can ensure that each high voltage fuse meets the required specifications and performance standards. Enhanced testing procedures include thermal analysis, electrical stress testing, and environmental exposure testing, which verify the fuse's ability to operate reliably under various conditions.
Benefits of Advancements in Materials and Manufacturing
The ongoing advancements in materials and manufacturing for HV fuses offer several significant benefits:
Improved Reliability and Performance: New materials can enhance the thermal stability, arc quenching capabilities, and overall durability of HV fuses. This translates to more reliable operation under challenging conditions and a longer service life.
Reduced Fuse Size and Weight: Advanced materials and manufacturing techniques can potentially lead to more compact and lightweight HV fuse designs. This can be particularly advantageous in applications where space constraints are a concern, such as within substations or electrical switchgear.
Enhanced Cost-Effectiveness: Advancements in manufacturing efficiency can potentially lower production costs for HV fuses. Additionally, longer service life and reduced maintenance requirements can contribute to overall cost savings.
Environmental Considerations: Research is ongoing into developing environmentally friendly materials and manufacturing processes for HV fuses. This can minimize the environmental impact of HV fuse production and disposal.
Challenges and Considerations for New Technologies
Despite the promising advancements, some challenges need to be addressed:
Material Characterization and Testing: Rigorous testing and characterization of novel materials are crucial to ensure their suitability for HV fuse applications. Understanding their long-term performance and behavior under various environmental conditions is essential.
Integration with Existing Systems: New HV fuse designs may require modifications to existing electrical equipment or protection schemes to ensure compatibility and optimal performance.
Standardization and Regulatory Approval: New materials and manufacturing processes may necessitate updates to existing industry standards and regulatory procedures. Ensuring safety and compliance with established regulations is critical.
Advancements in materials science and manufacturing processes have significantly influenced the development of high voltage fuses, leading to products that offer improved performance, reliability, and cost-effectiveness. These innovations not only benefit the electrical industry but also align with broader trends toward sustainability and smart grid integration. As technology continues to evolve, high voltage fuses will undoubtedly play a pivotal role in ensuring the safety and efficiency of electrical systems worldwide.